The Product Journey of the Janne Blazer and Bièl Pants Wool
Raw Materials - Sheep Farm
Australia
Our wool is sourced from Merino sheep in Australia. While the farm we work with practices mulesing-free methods, it is still in the process of obtaining official RWS certification. Achieving this certification can take several years, but in the meantime, the breeder is fully committed to ensuring the ethical treatment of their sheep. Mulesing-free means that no painful procedures are carried out, such as cutting skin from the sheep. This guarantees the mental and physical well-being of the Merino sheep. They are expected to receive their RWS certification in 2025.

Processing & Carding
Castanheira de Pera, Portugal
Once the wool arrives in Portugal, it is carefully stored and prepared for production. The wool is then put through the carding process, where it is transformed into a soft, uniform pulp by the action of combing machinery. This process helps align the fibers, which are then separated into small strands, preparing them for the next steps of production.
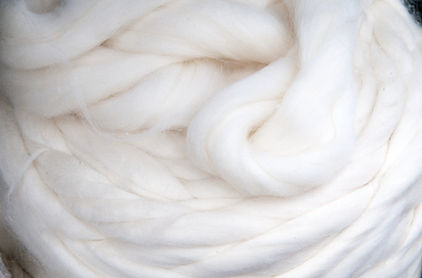
Spinning & Warping
Castanheira de Pera, Portugal
In this step, the strands are fed into spinning machines where they are stretched and twisted to create carded yarn. This yarn will eventually become the fabric of your suit.
The yarn is then stretched into long, parallel strands of thread, known as a warp, ready for weaving.
Weaving
Castanheira de Pera, Portugal
The warp threads are woven with weft threads to create fabric. The weaving process combines the different threads to produce the texture, thickness and durability of the wool fabric that defines our suits.

Dyeing
Castanheira de Pera, Portugal
Color is one of the most important aspects of your wool suit. The fabric is dyed to achieve the exact shade according to a panton colour we choose, matched in a laboratory to ensure consistency and vibrancy.
Finishing
Castanheira de Pera, Portugal
The fabric goes through a finishing process that involves two main parts:
-
Wet Sector: The fabric is washed and treated to give it a refined appearance.
-
Dry Sector: Special machinery is used to enhance the fabric’s softness, texture, and stability.
This step is essential to ensuring that the final fabric feels luxurious and has the perfect look and feel for a high-quality suit.
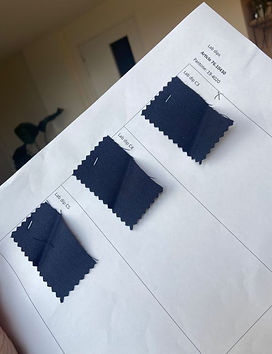
Manufacturing
Lousada, Portugal
The dyed fabric is sent to our tailoring manufacturer in Portugal. Our tailoring woven supplier is a family business producing the highest quality tailoring, with more than 30 year of experience. All of their tailored garments are produced in their own state-of-the-art factories in Portugal. Read more about our tailoring woven supplier on our partner page. The factory is a Sedex member and undergoes annual SMETA audits to ensure compliance with ethical trade standards.
Before cutting the fabric and sewing it into our Floria designs, there has been a whole process beforehand of fittings, adjusting patterns, an other fitting etc. This process takes up about 6 months.
Our partner Fous a Fous has sourced our natural Corozo buttons and zippers and our tailoring supplier has sourced the pocket and jacket lining. The lining was deadstock fabric and has been matched to our wool fabric. Our labels are made from certified cotton.
We always produce in small batches of 50 clothing pieces per color, and for the red color, only 26 pieces.
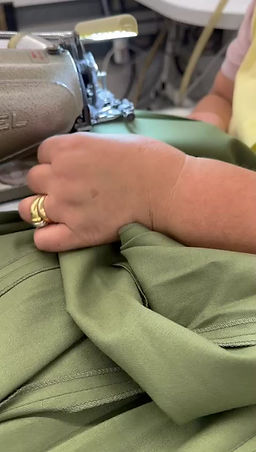
Ready to order
Almere, The Netherlands
After the Janne blazer and Bièl pants are ready and checked, the are send to Almere, The Netherlands. Founders Froukje and Fleur check all clothing, organize a photoshoot, write descriptions and publish the suits online. After you order they get another round of inspection and then get neatly packed and sent out by Froukje or Fleur. Ready to wear impact? Head over to the SHOP now.
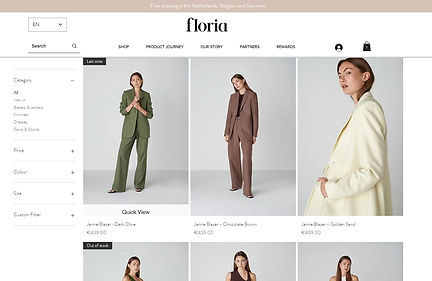